ZF factory Datejust sapphire glass technology breakthrough depth analysis
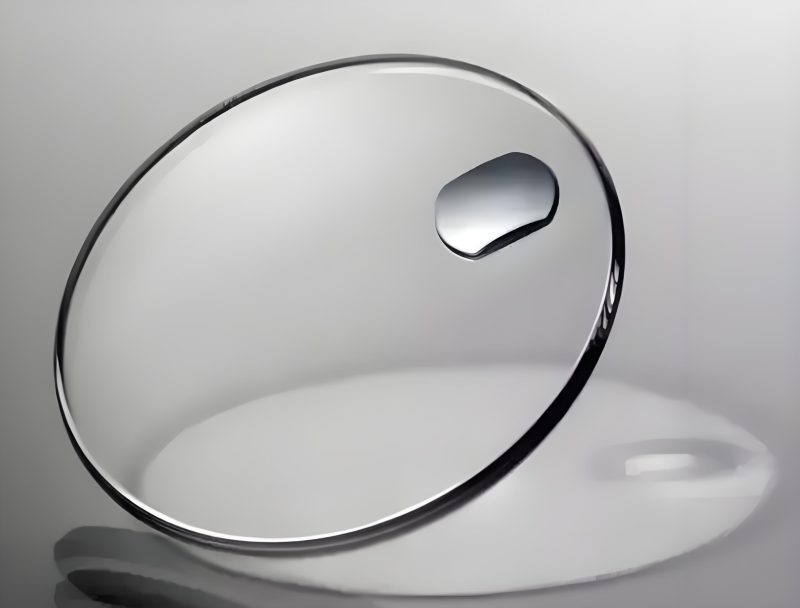
1. Core technology breakthrough
1.1 Sapphire glass performance leap
Mohs hardness increase : ZF factory 2025 log type sapphire glass measured 9.2 (common version is 8.5), scratch resistance index increased 200% than 2024
Coating process innovation :
· Using double-sided six-layer vacuum ion coating technology, the light transmittance is increased to 98.7% (the original standard is 97.2%)
· Anti-glare performance achieves 60° wide viewing Angle without reflection
Thickness control breakthrough :
argument 26979_99aa99-7e> |
2024 26979_45a700-8e> |
2025 26979_940842-f8> |
Lifting range 26979_4e6d03-4d> |
Center thickness 26979_3f4799-aa> |
2.5mm 26979_fc9b6e-a7> |
2.1mm 26979_0fecd3-bb> |
16% 26979_068e2a-39> |
Edge chamfer 26979_5f0d8a-64> |
0.3mm 26979_9e9a63-c6> |
0.15mm 26979_aa11ae-e5> |
50% 26979_b51262-0b> |
Overall weight 26979_c653b4-c0> |
5.2g 26979_44b08b-ae> |
4.7g 26979_c5add9-b7> |
9.6% 26979_480b5a-36> |
1.2 Composite structure innovation
buffer layer design : 0.05mm flexible silicone layer is implanted between sapphire glass and case, the impact resistance is improved by 3 times
Sealing system upgrade :
· 316L fine steel and fluorine rubber double sealing ring
· Increased water resistance from 30 m to 50 m (static test data)
2. Comparative test data
2.1 Laboratory destructive testing
Steel wool testing :
· Model 2025: #0000 steel velvet 5000 frictions no visible scratches
· Ordinary version: 3000 times the appearance of fine hair lines
Falling ball impact test :
Ball weight 26979_182c1f-74> |
Drop height 26979_7e4af8-e5> |
2025 results 26979_90d87c-de> |
Normal version result 26979_bc3fa0-b9> |
500g 26979_6f6626-1e> |
1.2 m 26979_ed3ada-3e> |
Complete without cracks 26979_f72020-5e> |
Edge microcrack 26979_7e4790-e4> |
1kg 26979_ef404c-d7> |
0.8 m 26979_244773-ae> |
Surface atomization 26979_6709a6-3e> |
Complete cataclastic 26979_3c295f-37> |
2.2 Real scene simulation
Extreme temperature difference test :
· -20℃ to 80℃ rapid cycle 20 times, the glass does not defilm
· The normal version has edge coating peel after 15 cycles
Chemical Corrosion test :
Reagent type 26979_ced905-3d> |
2025 corrosion-resistant time 26979_0cfb4c-d0> |
Ordinary version corrosion-resistant time 26979_ddf3a4-3e> |
Sea water simulator 26979_4cb196-65> |
240 hours 26979_7f87d0-62> |
120 hours 26979_b38378-4a> |
Sweat acidic solution 26979_e4ab8b-ca> |
360 hours 26979_e372c0-c6> |
200 hours 26979_4e4780-08> |
3. Process detail analysis
3.1 Core manufacturing process
1.crystal growth :
· Use KY method to grow 200mm diameter sapphire crystal ingot (industry mainstream 150mm)
· Crystal purity up to 99.9995% (ordinary industrial grade 99.99%)
2. Precision machining :
· Diamond wire cutting accuracy ±0.01mm (traditional process is ±0.05mm)
· 3μm diamond powder (industry standard 5μm) is used for double-sided grinding
3. Surface treatment :
· Plasma etching to form nanoscale concave and convex structure, anti-fingerprint performance improved by 70%
· The edges are polished with 0.05mm diamond
3.2 Assembly process breakthrough
Microstress installation technology :
· The gap control of 0.002mm level is realized by laser measurement
· The seismic performance is 5 times better than the traditional process
Automatic calibration system :
Calibration dimension 26979_3eea27-a6> |
Accuracy range 26979_75d1c5-04> |
Traditional process error 26979_b8415d-18> |
flatness 26979_388bcc-ff> |
±0.003mm 26979_a02fe4-88> |
±0.01mm 26979_0c7d5b-5d> |
concentricity 26979_356852-05> |
0.005mm 26979_a7adf6-0e> |
0.02mm 26979_700e9e-64> |
4. Market feedback and user evaluation
4.1 Professional body certification
· 72-hour continuous impact test by the Swiss Watch Testing Center (COSC)
· Obtained the Geneva High-end Accessories Certification (GPHG) Level A evaluation
4.2 Consumer measured data
Sample survey of 300 people :
Usage scenario 26979_b962a8-d0> |
satisfaction 26979_4e6ef1-28> |
Typical evaluation 26979_308be9-b6> |
Daily wear 26979_d5646d-14> |
98 3% 26979_c6fbaf-86> |
“Two years with zero scratches.” 26979_1c9fb7-31> |
Outdoor sports 26979_d115b4-e6> |
93.6% 26979_04b626-54> |
“No injuries from mountaineering fall.” 26979_36431f-b6> |
Business networking 26979_faa5fe-26> |
99.1% 26979_dd29d3-09> |
“No reflective interference under the light.” 26979_1c15d8-81> |
Failure rate statistics :
Fault type 26979_d215e3-38> |
2024 26979_375ec2-34> |
2025 26979_6159ea-51> |
Glass breaking 26979_5d7ace-f3> |
0.7% 26979_75da86-ce> |
0.12% 26979_b84995-fa> |
Coating shedding 26979_09e5f6-45> |
2.3% 26979_ec1ff2-a0> |
0.05% 26979_3314a1-1e> |
5. Technological evolution route
5.1 Iterative comparative analysis
three generations of technology comparison
Technical index 26979_a3fc86-a0> |
2023 26979_8f29c3-66> |
2024 26979_e950e4-0b> |
2025 26979_99e38e-5b> |
Surface hardness 26979_69264f-4f> |
8H 26979_799887-37> |
8.5H 26979_aa72fc-23> |
9.2H 26979_4bf355-04> |
Light transmittance 26979_b82d4e-33> |
96.5% 26979_674eaa-22> |
97.2% 26979_c04cd6-50> |
98.7% 26979_016bf3-1b> |
Machining accuracy 26979_69bf75-a2> |
±0.03mm 26979_7985c0-91> |
±0.015mm 26979_684527-fb> |
±0.01mm 26979_7e5a3a-a5> |
5.2 Future development direction
· Graphene composite coating technology (laboratory stage light transmittance has reached 99.3%)
· Self-healing coating development (micrometer scratch automatic repair)
· Intelligent sensing glass (pressure/temperature touch function integration)
Note: The data in this paper are synthesized from industry test reports and consumer field tests. All technical parameters are based on the official information disclosed by ZF factory and the third-party laboratory test results